Stock Mapping voor interne logistiek
Uit kostenoogpunt streven bedrijven naar een zo laag mogelijke voorraadhoogte. Want werkkapitaal moet niet onnodig vastzitten in voorraden, maar gebruikt worden om te investeren en te groeien. Tegelijkertijd zijn voorraden nodig om onzekerheden en doorlooptijden in de keten op te vangen. De optimale voorraadhoogte is een zo laag mogelijke voorraad waarbij onzekerheden en doorlooptijden kunnen worden opgevangen. Hiertoe is het belangrijk om de pijnpunten in het interne logistieke proces op te zoeken en de achterliggende problemen te analyseren.
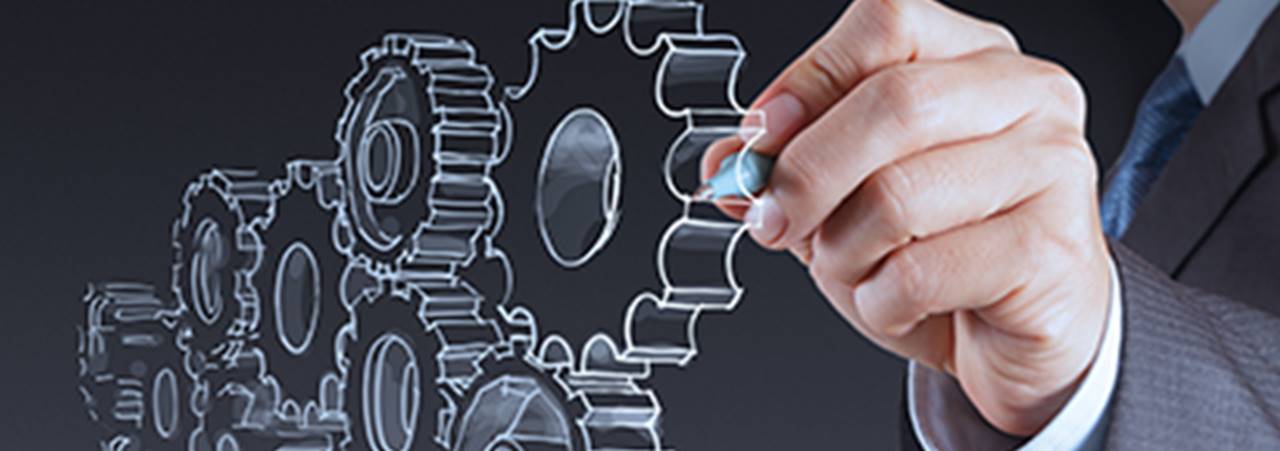
Interne logistieke processen
Het niet op orde of onder controle zijn van de interne logistieke processen resulteert vaak in voorraden op verschillende plaatsen in het proces waar ze niet nodig zijn. In de praktijk heb ik bedrijven gezien waar het interne logistieke proces niet op orde was, met als gevolg dat vanwege de slechte leverbetrouwbaarheid voorraden werden aangelegd in het gehele proces. Dit resulteert inderdaad in goede leverbetrouwbaarheid, maar ook in hogere kosten. En als het logistieke proces niet op orde is, kan de afdeling planning het ook niet goed aansturen. Dit is het typische schoolvoorbeeld van een boot die veilig over een rivier vaart, omdat het waterniveau (voorraad) hoog is. De rotsen (problemen in het proces) leveren geen probleem op. Maar de kunst is juist om de rotsen te vinden en verwijderen, of creatieve oplossingen te vinden. De pijnpunten komen pas boven water als het voorraadniveau zakt!
Overzicht krijgen door stock mapping
Om de pijnpunten in het interne logistieke proces op te zoeken en te analyseren wat het achterliggende probleem is, vind ik het fijn om voorraden eerst inzichtelijk te maken in het proces. Dit noem ik 'stock mapping'. Deze eerste stap is naar mijn mening erg belangrijk omdat het vaak al goed laat zien waar de knelpunten in het proces zitten. Met dit overzicht kan helder en gemakkelijk worden gecommuniceerd naar andere afdelingen.
Voor stock mapping is nodig:
- Een Bill Of Material (BOM)
- Productiestappen
- Leadtimes en/of productietijden
- Voorraden, 'Work in progress'- ofwel WIP-voorraden, werkorders
Stel, we hebben een productiebedrijf dat product X maakt. Dan kun je de volgende stappen doorlopen:
- Door de BOM van product X uit te klappen, ontstaat een overzicht van artikelen die nodig zijn om product X te maken. Deze artikelen kunnen ook weer worden uitgeklapt als ze een onderliggende BOM hebben. Deze BOM(s) geef je grafisch weer met behulp van bijvoorbeeld Excel.
- Vervolgens verwerk je in hetzelfde overzicht de productiestappen die nodig zijn om om product X en de bijbehorende artikelen te maken.
- Leadtimes en/of productietijden bij de productiestappen zetten geeft inzicht in onder andere het kritieke pad en de knelpunten (theory of constraints) in het proces.
- Koppel nu de voorraden van de artikelen in het overzicht. Deze informatie is normaal gesproken te vinden in het bedrijfsinformatiesysteem (ERP/MRP). Nodig zijn de voorraden van de artikelen en van product X. Daarnaast kan met behulp van werkorders de WIP-voorraad worden berekend. Het is aan te raden om deze gegevens via de IT-afdeling te verkrijgen. Die kan vaak gemakkelijk gegevens exporteren die je vervolgens via een macro in Excel kunt inladen.
- Tot slot kan je verschillende berekeningen in het overzicht gebruiken om bijvoorbeeld uit te rekenen hoeveel eindproducten er in het hele productieproces zitten als alle WIP-voorraden verwerkt zijn.
Dit zou het startpunt van de analyse moeten zijn. Dit overzicht geeft direct aan waar de knelpunten zich bevinden. Ik heb tijdens een opdracht gemerkt dat dit erg fijn werkt en dat je andere afdelingen zo gemakkelijker kunt meenemen.